 |
This is Phil Lowe in the bench room. |
A place once alive with passion, dedication, and love for the craft and art of furniture making. The Furniture Institute of Massachusetts—FIM—was more than just a school; it was a sanctuary for those who truly wanted to learn the trade the right way.
Just today, I heard from a former student who attended one of the workshops. He told me how much fun he had—even though it was the hardest class he’d ever taken. Yet, he misses the school. That sentiment makes me happy, because I loved FIM deeply. It was a joy and privilege to walk those halls and be part of that world.
For those who never had the chance to step foot inside, let me try to paint the picture:
You’d walk in and see the drafting room—four full-sized drawing boards lined up, surrounded by a library filled with books ready to be studied and referenced.
Step out into the hallway, and there it was: a full wall of incredible sample work. Many were period reproductions, and most were done by Phil Lowe’s hand over the decades. It was like a museum in motion.
The first door on the right was Phil’s office—a place he had a love-hate relationship with. It was filled with paperwork, emails, chasing down students, and billing. A necessary evil, as he might say.
Farther down the hall was a bank of drawers where Phil kept his vast collection of veneer. I now have those drawers, and I treasure them. I open them often, and when I do, I think of Phil.
Across from those drawers was the finishing room. Right in front of that space stood a gorgeous period casing—crafted by Phil for a client in NYC who later wanted a different version. So Phil hung the original in the school for us to enjoy. A daily reminder of his craftsmanship.
Next came the heart of it all: the bench room. Nine workbenches, each paired with its own bookcase. This was where the real magic happened—joinery echoing with the rhythm of mallets and chisels, shavings on the floor, the distinct scent of hide glue in the air. Throw in the smell of coffee, and it was heaven to me.
Toward the back wall of the bench room sat Phil’s personal bench, backed by a wall of tools he had collected and used throughout his career. It was breathtaking. If I had the space, I would’ve taken that wall with me when the school closed. Now, I keep it alive through photos and memory. I spent many hours sharpening those tools—and learned so much in the process.
Then there was the small machine room, affectionately referred to as “The Finish Room.” It held only the essentials: a planer, jointer, 10” table saw, scroll saw, grinders, a Bridgeport (used occasionally), and a portable bandsaw. Phil always said, “This is all you need. Everything else is a luxury that just makes things easier.”
Beyond that was the roughing room—filled with vintage, heavy-duty stationary machines. Most were 3-phase: Oliver planer and jointer, a DeWalt 18” bandsaw, a Fay & Egan 36” bandsaw, Delta and General lathes, an Oliver table saw, a swing saw, foot pedal mortiser and more. At first, they were intimidating, but with respect and understanding, they became old friends.
Behind the machine room was the lumber rack—a beautiful collection of material stored in compartments and loft spaces. Some belonged to Phil, some to students. Walking down the ramp to see the lumber was always a highlight. And off to the side was the scrap shelf—where you could find hidden gems if you took the time to look.
There was also a small mechanical room for tool repairs, and a wall lined with shaper knives.
What a space. What an experience. I wish you all could see it today. I’ll add some images to the post to help keep the memory alive.
I miss the man. I miss the legend. Phil Lowe was my mentor first, a friend second—and as he used to joke, I was “the Puerto Rican son he never had.” That was an honor. But don’t get it twisted—I paid for everything. Phil was a true Yankee, through and through, and I loved that about him.
If you want to experience a bit of his brilliance, search “Phil Lowe Woodworking” on YouTube. There’s a treasure trove of videos where you can learn from him directly. I still watch them—both to hear his voice and to sharpen my own teaching skills.
Until next time.
—Freddy
 |
The school sign! Which I own and will hang again.
|
 |
Phil as a student at NBSS |
 |
Phil in the bench room with his tool wall behind him a FWW shot. |
P
 |
The ramp to the big machine room! |
 |
Phil’s area and work bench. |
 |
Bench room! |
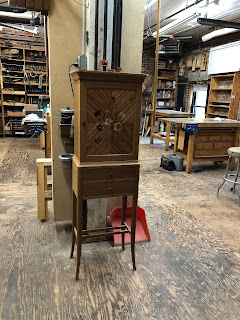 |
Phil’s last piece he made. |
 |
The museum hall of samples. |
 |
Drafting room! |
 |
The first time I met Phil! |
 |
Phil as a teacher at NBSS! |
 |
Phil early on as a teacher at NBSS
|